摘要
電子零件與電路板裝連技術簡介
普通插裝技術(Through Hole Technology,THT)生產製程中有很長一段時間是採用的是人工插裝,到後面才出現了自動化的插裝機。雖然SMT(表面組裝技術,Surface Mount Technology)出現了幾十年,仍然無法完全替代普通插裝技術(THT),因為有些元器件還無法片式化,所有在現代電子裝聯技術中,普通插裝技術仍然不可或缺。
何謂THT(普通插裝技術,Through Hole Technology)
普通插裝技術(THT,Through Hole Technology)電子零件一開始是使用普通插裝技術(THT,Through Hole Technology),它的特點元器件體積大集成度不高,插裝技術生產速度比較慢。THT(普通插裝技術,Through Hole Technology)是將長引進的組裝元器件,插裝到電路板上,通過波峰焊等方式加以焊接組裝的電路裝聯技術。
何謂SMD(Surface Mount Device,表面貼焊零件)
指可以使用在SMT製程或技術的電子零件。和通孔插裝技術(THT,Through Hole Technology)的最大不同處在於,表面黏著技術(SMT)不需為元件針腳預留對應貫穿孔,而表面黏著技術(SMT)元件尺寸也比通孔插裝技術(THT)微小許多。藉由應用表面黏著技術可以增加整體處理速度,由於零件的微小化及密度的增加電路板的缺陷風險因而隨之提高,在任何表面黏著技術的電路板製造過程,錯誤偵測已經變成必要的一環。
何謂SMT(Surface Mount Technology)?
是一種把電子零件焊接在電路板(PCB, Printed Circuit Board)表面的一種技術,起源於60年代,最初由美國IBM公司進行技術研發,之後於80年代後期漸趨成熟。此技術是將電子元件,如電阻、電容、電晶體、積體電路等等安裝到印刷電路板上,並通過釺焊形成電氣聯結。
採用SMT技術有何優點與好處?
- 電子產品可以設計得更輕薄短小:
零件變得更小,電路板的使用面積也會比以前的通孔零件來的小。 - 可以設計出更高端的產品:
因為SMD小與薄,讓電子產品應用在更多的零域。如微型機器人、更快速的CPU(中央處理器),更適合隨身攜帶的電子產品。 - 適合大量生產:
因為SMT技術摒除了大部分的人工插件作業,改以機器來置放電子零件,所以更適合用來大量生產出高品質的產品,而且製程也比通孔插件更穩定。 - 生產成本降低:
基本上就是降低了人力及工時。因為通孔零件靠人工置件,而SMT則改為機器置件。
SMT加工中常見的BGA種類
SMT加工廠的BGA類封裝(Ball Grid Array),按其結構劃分,主要有塑料BGA(P-BGA)、倒裝BGA(F-BGA)、載帶BGA(T-BGA)和陶瓷BGA(C-BGA),BGA(即Ball GridAray)有多種結構,如塑封BGA (P-BGA)、倒裝BGA( F-BGA )、載帶BGA(T-BGA)和陶瓷BGA(C-BGA),lPBGA(Plastic塑料封裝的BGA),lCBGA(Ceramic陶瓷封裝的BGA),lCCGA(Ceramiccolumn陶瓷柱狀封裝的BGA),lTBGA(Tap BGA載帶狀封裝的BGA),lCSP(Chip scale BGA或μBGA)。
甚麼是BGA?
BGA(Ball Grid Array,球柵陣列封裝)技術的研究始於60年代,最早被美國IBM公司採用,是一種全新的設計思維方式,它採用將圓型或者柱狀點隱藏在封裝下面的結構,引線間距大、長度短,消除了精細間距器件中由於引線問題而引起的共平面度和翹曲的問題。引腳水平面統一性較QFP(方型扁平式封装技術, Quad Flat Package)容易保證,因為焊球在溶化以後可以自動補償晶片與PCB之間的平面誤差。圖1為BGA元件封裝物理結構及外形。
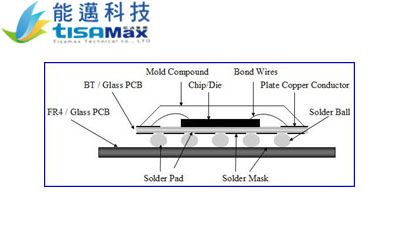
圖1. BGA元件封裝物理結構及外形
BGA焊接不良的診斷與處理
BGA(Ball Grid Array,球柵陣列封裝)的焊接是PCBA加工重要工序,但由於BGA焊後檢查和維修比較困難,必須使用X射線透視才能確保焊接連接的可靠性。所以在PCBA(Printed circuit board assembly,印刷電路板+組裝) 加工的回流焊接時對BGA(Ball Grid Array,球柵陣列封裝)焊接不良的診斷就至關重要了。
BGA典型缺陷有:空洞、脫焊焊點、錫橋和短路、不對準、開路(冷焊點)、移位、橋連、焊點邊緣模糊、吹孔、結晶破裂、濺錫,而X 光2D/3D CT(3D X ray CT)檢查機已成為在成功的焊接運行和可靠的焊點取得實際的認可驗證設備。
空洞:焊接空洞是由加熱期間焊錫中夾住的化合物的膨脹所引起的。雖然有空洞的BGA焊接點可能表示會引起將來失效的工藝問題。
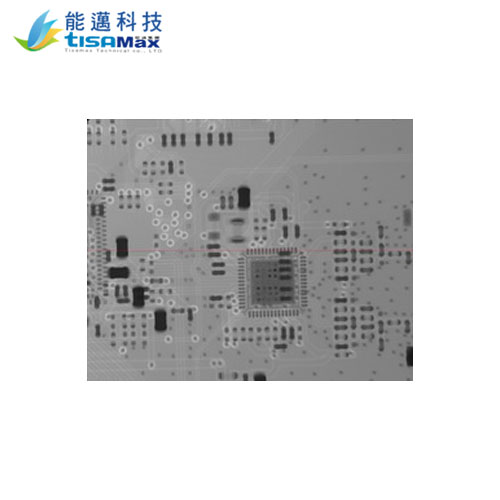
圖2. BGA的焊接空洞
IPC-7095中規定:焊盤層的空洞面積不能大於焊球面積的10%,即空洞直徑不能超過焊球直徑30%;焊料層(空洞位於焊球中間)的空洞面積不能大於焊球面積的25%,即空洞直徑不能超過焊球直徑的50%。空洞面積占焊球面積的比例可以按如下方法計算:如果空洞直徑是焊球直徑的50%,那麼空洞面積是焊球面積的25%。
目視:對於BGA等封裝陣列來說,在沒有檢查設備的情況下,先目視觀察最外面一圈焊點的塌陷是否一致,再將晶片對著光看,如果每一排每一列都能透過光,那麼可以斷定沒有連焊,有時尺寸大一點的焊球也可以看見。但是不能檢測到內部缺陷(如空洞)。
錫橋和短路:焊錫由焊墊流至另一個焊墊形成一座橋或短路,當過多焊錫在接觸點或者當焊錫放置不當時,經常發生橋接和短路。在接收標準中,不能存在短路或橋接的焊點,除非它們專門設計成底層電路或BGA。
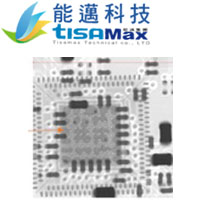
圖3. BGA 短路(錫橋,橋接)
橋接(錫橋)診斷:錫膏、錫球塌陷,印刷不良。
橋接(錫橋)處理:調整溫度曲線,減小回流氣壓,提高印刷品質。
不對準:X光圖象將清楚地顯示是否BGA球沒有適當地對準PCB上的焊盤。不對準是不允許的。
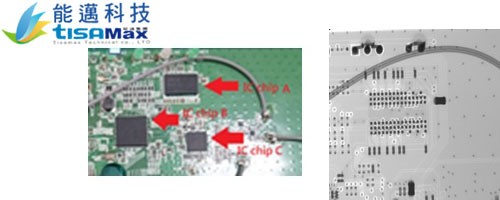
圖4. BGA錫球沒有適當對準PCB的焊盤
開路和冷焊點:當焊錫和相應的焊盤不接觸或者焊錫不正確流動時,發生開路和冷焊點。這種情況不允許。
冷焊:焊點表面無光澤,且不完全溶接。
冷焊診斷:焊接時熱量不足,振動造成焊點裸露。
冷焊處理:調整溫度曲線,冷卻過程中,減少振動。
位移(偏移):BGA焊點與PCB焊墊錯位。
位移(偏移)診斷:貼片不准,輸送振動。
位移(偏移)診斷:加強貼片機的維護與保養,提高貼片精準度,減小振動誤差。
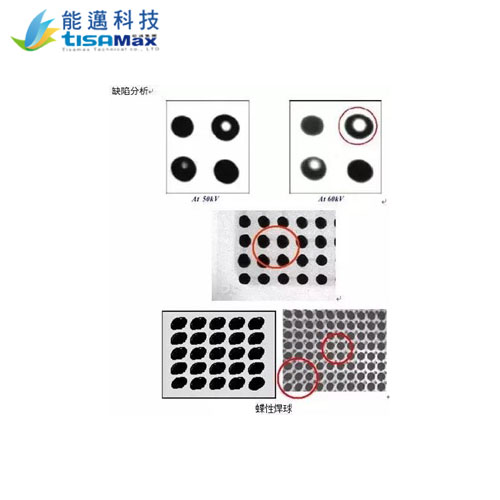
焊點邊緣模糊(HIP,Head-In-Pillow,枕頭效應,雙球效應):BGA焊接後最主要的品質問題幾乎都集中在HIP (Head-In-Pillow,枕頭效應,雙球效應)。這是因電路板(PCB)流經Reflow的回焊高溫區時容易造成PCB板材及BGA本體變形,在錫膏及BGA錫球熔融成液態時互相分離沒有接觸在一起,等電路板溫度開始下降並低於焊錫的熔點後,PCB及BGA 本體的變形量也漸漸變小,可是錫膏及錫球已經凝結變回固態,以致形成雙球重疊的假焊現象,這就是有名的HIP(Head-In-Pillow,枕頭效應,雙球效應)。
而90%以上的HIP(Head-In-Pillow,枕頭效應,雙球效應)大多出現在BGA的最外排錫球或其四個角落區域,這是因為BGA封裝對角線的距離最長,相對的變形也就最嚴重,變形量第二嚴重的地方則是BGA最外排的錫球。
吹孔:錫球表面出現孔狀或圓形陷坑。
吹孔診斷:在回流焊接時,BGA錫球內孔隙有氣體溢出。
吹孔處理:用X-Ray檢查原材料內部有無孔隙,調整溫度曲線。
結晶破裂:焊點表面呈現玻璃裂痕狀態。
結晶破裂診斷:使用金為焊墊時,金與錫/鉛相熔時結晶破裂。
結晶破裂處理:在金的焊墊上預先覆上錫,調整溫度曲線。
濺錫:在PCB表面有微小的錫球靠近或介於兩焊點間。
濺錫診斷:錫膏品質不佳,升溫太快。
濺錫處理:檢查錫膏的儲存時間及條件,按要求選用合適的錫膏,調整溫度曲線。
人工X射線檢測
使用人工X射線檢測設備,需要逐個檢查焊點並確定其是否合格。該設備配有手動或電腦輔助裝置,以便更好地進行檢測和攝像。詳細定義的標準或目視檢測圖表可指導評估檢測結果。通常的目視檢測要求培訓操作人員,並且容易出錯,且人工設備並不適合對全部焊點進行檢測,只適合製程鑑定和製程故障分析。
自動X射線檢測
自動檢測系統能對全部焊點進行檢測,通常用於產量高且品種少的生產設備上,具有高價值或要求可靠性的產品也需要進行自動檢測。檢測結果與需要返修的電路板一起送給返修人員,並提供相關的統計資料,用於改進生產工藝。
自動檢測系統需要設置正確的檢測參數。大多數新系統的軟體中都定義了檢測指標,但必須重新制訂,定義所要檢查焊點的面積和高度或把焊點剖成不同的截面,以適應生產工藝中所特有的因素,否則可能得到錯誤的信息且降低系統可靠性。
自動檢測系統有兩種工作模式:直射式X射線測試系統和斷面X射線自動測試系統。直射式X射線系統源於X射線束沿通路複合吸收的特性,對SMT的某些焊接,如單面PCB上的J型引線與細間距QFP(方型扁平式封装技術, Quad Flat Package)等,是測定焊接質量最好的方法,且設備比較便宜,但它卻不能區分垂直重疊的特徵。當PCB兩面的同一位置都有元件的情況下,這些焊料形成的陰影會重疊起來,分不清是那一層的問題;另外當BGA(Ball Grid Array,球柵陣列封裝)器件的焊縫被其內部引線遮掩時,也存在上述這個問題。斷面X射線測試系統克服了這些問題,它設計了一個聚焦斷面,並通過使目標區域上下平面散焦的方法,將PCB的水平區域分開。該系統的成功在於只需較短的測試時間,就能準確檢測出焊接缺陷。對於小體積的複雜產品,最好使用斷面X射線測試系統。雖然所有方法都可檢查焊接點,但斷面X射線測試(3D X ray CT)系統提供了一種非破壞性的測試方法,可檢測所有類型的焊接質量,並獲得有價值的調整組裝工藝的信息。
X光2D/3D CT在電子產業IPC標準及其他應用
- IC封裝中的缺陷檢測,如﹕層剝離、爆裂、空洞、打線完整性檢測。
- PCB製程中可能產生的缺陷,如﹕對齊不良或橋接以及開路。
- SMT焊點空洞現象檢測。
- 各式連接線路中可能產生的開路、短路或不正常連接的缺陷檢測。
- 錫球陣列封裝及覆晶片封裝中錫球的完整性檢測。
- 密度較高的塑膠材質破裂或金屬材質空洞檢測。
- 晶片尺寸量測、打線線弧量測、元件吃錫面積比例量測。
- IC 封裝中的缺陷檢驗如:打線的完整性檢驗、電測異常 (Open/Short) 、黑膠的裂痕、銀膠及黑膠的氣泡。
- 印刷電路板及載板製程中可能產生的缺陷,如:線路對齊不良或橋接以及開路、電鍍孔製程品質檢驗、多層板各層線路配置分析。
- 各式電子產品中可能產生的開路,短路或不正常連接的缺陷檢驗。
- 錫球陣列封裝及覆晶片封裝中錫球的完整性檢驗:如錫球變形、錫裂、錫球空冷銲、錫球短路、錫球氣泡。
- 密度較高的塑膠材質破裂或金屬材質空洞檢驗。
- 各式主、被動元件檢測分析。
- 各種材料結構檢驗分析及尺寸量測。
- PCB及載板(Substrate)製程中產生的缺陷,如線路製程不良、橋接、開路、電鍍孔製程品質檢驗、多層板各層線路配置分析。
- 電子產品開路(Open)、短路(Short)或不正常連接的缺陷分析。
- 錫球陣列封裝(BGA)及覆晶片封裝(Flip Chip)中錫球的完整性分析,如錫球變形、錫裂、錫球空冷銲、錫球短路、錫球氣泡。
- 密度較高的塑膠材質破裂或金屬材質空洞檢驗。
- IC封裝中的缺陷檢驗如:打金線的完整性檢驗、黑膠的裂痕、銀膠及黑膠的氣泡。
- 印刷電路板及載板製程中可能產生的缺陷,例如:線路對齊不良或橋接以及開路、電鍍孔製程品質檢驗、多層板各層線路配置分析。
- 各式電子產品中可能產生的開路,短路或不正常連接的缺陷檢驗。
- 錫球陣列封裝及覆晶片封裝中錫球的完整性檢驗:比如錫球變形、錫裂、錫球空冷銲、錫球短路、HIP、NWO、錫球氣泡。
- 密度較高的塑膠材質破裂或金屬材質空洞檢驗。
- 各式主、被動元件檢測分析。
- 各種材料結構檢驗分析。如:合金的材質分析、玻璃纖維編織角度分析
- 逆向工程
【3D X-Ray CT】除了可以拿來檢查一些肉眼看不到的地方,還可以做逆向工程分析,如有些使用超音波黏死殼子或是某些特殊技巧防止拆解工藝,大部分都可以使用【3D X-Ray CT】將之一層一層解開。 - 成品檢查
一般用在精密機械加工件,有些尺寸及精度要求比較高的工件,可以用【3D X-Ray CT】來做全尺寸檢查,合成3D圖形後可以與原來的3D規格檔做比較,從而判斷允收或不良需要重工與否。